In our latest Applications Insight, we are focusing on protective fabrics, specifically for the emergency services and military.
Police, fire and rescue, paramedics and armed forces personnel play a pivotal role, and come into contact with a wide variety hazards in their day-to-day work, from the environment they are operating in, to the physical threat from situations that occur. These conditions present complex challenges for the garments and kit they wear, which need to perform for function and protection as well as comfort.
Read on to learn more, and then get our free Lab Manager’s Guide to Protective Wear Testing.
Emergency services and military uniforms - the performance challenge
The biggest challenge for these garments is the need to use fabrics that perform for protection, strength and durability, whilst providing wearer comfort.
For example, let’s consider a police uniform, which needs to be multi-purpose; professional in appearance and practical, while providing day-to-day comfort. However, it also needs additional properties when more strenuous physical activity is required, with performance attributes more akin to sportswear such as stretch, good moisture management and drying rate, or being waterproof yet allowing the skin to breathe.

“We know that the right workwear can limit the odds and severity of preventable work-related injuries, so first responder and military wear needs to incorporate the highest quality protective fabrics possible, to guarantee improved health and safety to the wearer along with a durability and a superior comfort.”
Let’s take a look at each area in more detail:
Movement
Flexibility of movement is a challenge, as often these uniforms require heavier materials and have multiple pockets, attachments and belts. Comfort stretch fabrics are now more widely used to ensure superior wearer comfort, moisture management and to provide the ability to move more freely.
Protection
Most protective workwear kit today incorporates specialised fabrics, using a combination of polyester and cotton fibres to enhance tensile strength and performance. Wearer protection is further enhanced using laminated, waterproof, and windproof solutions. A layer system is often critical, take the example of a firefighter working in extreme heat where a fabric must be resistant to flame and water yet be effective in allowing perspiration to escape, thus protecting the wearer from heat damage such as steam burning caused by the heating of trapped moisture.

Comfort
Comfort testing in textiles can be challenging, due to the subjective nature of what ‘comfort’ means to each individual. However, comfort can be generalised to include anything that affects how the wearer feels, both physically and mentally. This can include the fit of a garment, the dissipation of heat and moisture, the breathability of the material and so forth. If a wearer feels discomfort, this can lead to reduced concentration, lower mood and irritability, creating distractions for the wearer, which can ultimately have a negative impact on both the wearer, and subsequently the safety of the public in critical situations.
Function
The functional elements need to be tested to ensure durability in the field, including in wet conditions to reflect real-life wear of clothing, footwear, gloves and other accessories.
Features such as zips, buttons, pockets, elbow/shoulder patches, badge tabs and nameplates, add to a uniform’s practicality and need to be tested for strength of attachment and durability.
Additional properties required of these functional fabrics could also include:
- Built-in soil and stain release technology
- Custom finishes for wrinkle resistance and easy care
- Advanced odour control
- Deep-dye process for fade-resistance
Testing performance
Today’s emergency services garments and protective clothing need to include fabrics that are not only durable but are soft to the touch, retain their shape, and outperform other textiles for strength, but also incorporate technical textiles for greater protection and comfort. In order to meet the required criteria, garments need to integrate high-performance protective fabrics that offer excellent protection, increased breathability, and superior mechanical properties in a variety of environments and extreme conditions.
This is not a simple task and it requires close attention to detail in the testing of these materials and garments to specific standards during R&D and production to ensure effective performance, and importantly the safety and wellbeing of personnel in roles such as first responders and the armed forces.
Meet the Performance Range of test instruments
The James Heal performance testing range is ideal for testing the complex requirements of technical and performance textiles used in emergency services and the military.

More traditional textile testing covered by James Heal instruments for protective wear include:
- Flame resistance – FlexiBurn
- Wear and abrasion - Martindale
- Burst resistance - TruBurst
- Water resistance – Spray Rating Tester
- Strength and compression - Titan, e.g. for material strength or tests for buttons, epaullettes, patches etc.
- Tear testing - ElmaTear
- Colour fastness to light and laundering – TruFade and GyroWash
- Thermal conductivity / thermal effusivity
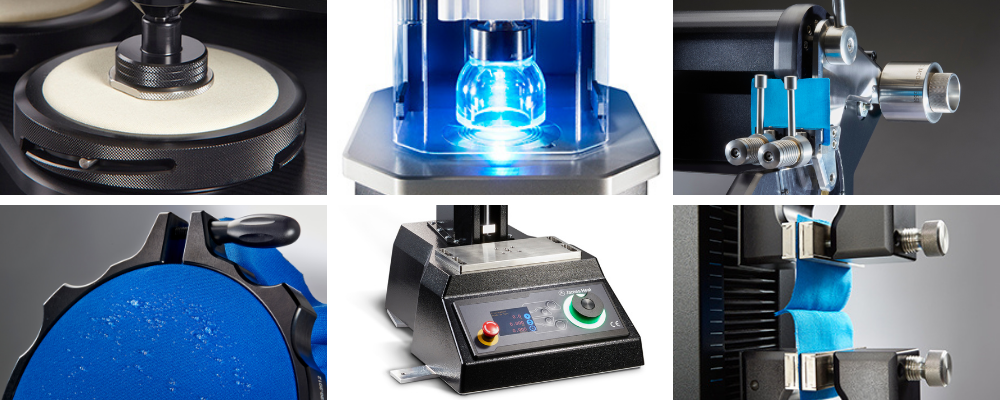
Additional resources
Want to learn more? Access our free Lab Manager’s Guide to Protective Wear Testing.
For further insight read our related Applications Insight: Military Textiles article, which covers this aspect in more detail.
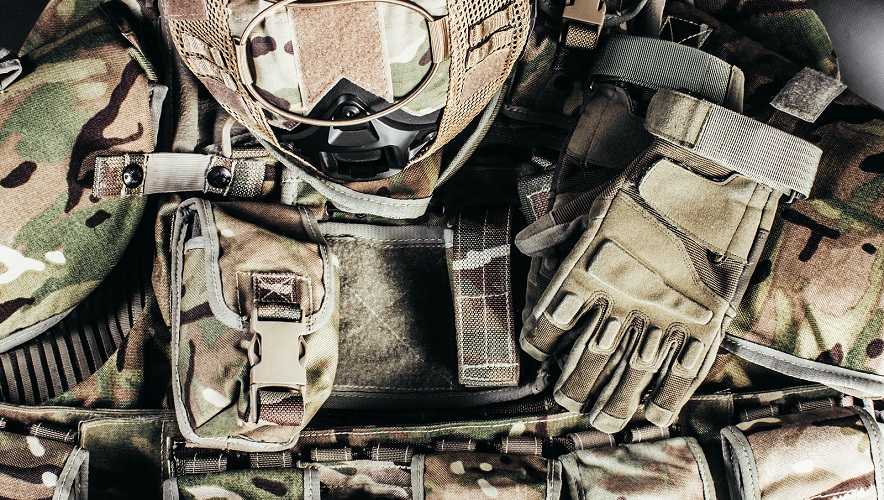