In our latest customer case study, we spoke with Laboratory Coordinator Henrik Zeh, from Mascot International A/S, to discuss the importance of quality control and using the right testing instruments.
At the height of growth in protective workwear
Mascot International A/S is an international, family-owned business, which develops, manufactures and markets high quality workwear and safety footwear. For many years, the company has experienced rapid growth in revenue - and it’s showing no signs of slowing down.
Mascot is presently undergoing a period of significant growth. With more than 3,500 employees across Europe and Vietnam, Mascot has become a leader within the workwear market. The surge in demand for high quality workwear and safety footwear, is largely being driven by tighter Health and Safety legislation, and a shift in employers’ (and employees’) attitudes to safety and wellbeing at work.
Whilst the Covid-19 pandemic made demand for disposable personal protective wear soar to record levels, the wider workwear and safety wear sector has also continued to grow, with Europe’s imports growing at a 4.8% annual average, and an expected CAGR of 6.9% from 2021 to 2028.
The continued growth in this market has further emphasised the need for accurate, reliable and consistent testing on the textiles, materials and garments used. And this is where James Heal comes in…
The Mascot Lab: a long-standing partnership

Henrik Zeh, Lab Coordinator at Mascot“We conduct our R&D testing here in our head office lab to ensure speed of decision making and being closer to the test."
Mascot has worked with James Heal for over 20 years, using various testing instruments such as Crockmeter, Gyrowash, Titan, Martindale, Orbitor, and the Spray Rating Tester, conducting much of their research and development testing at their head office lab in Denmark, with Vietnam’s factory lab being the base for the brand’s quality assurance testing.
“We conduct our R&D testing here in our head office lab to ensure speed of decision making and being closer to the test. When we’re developing a new fabric, we want to see how it will perform for its intended purpose”, explains Henrik. “Rather than testing the finished garment, here in Denmark we experiment with new development fabrics, such as those with recycled materials or technical functionality.”
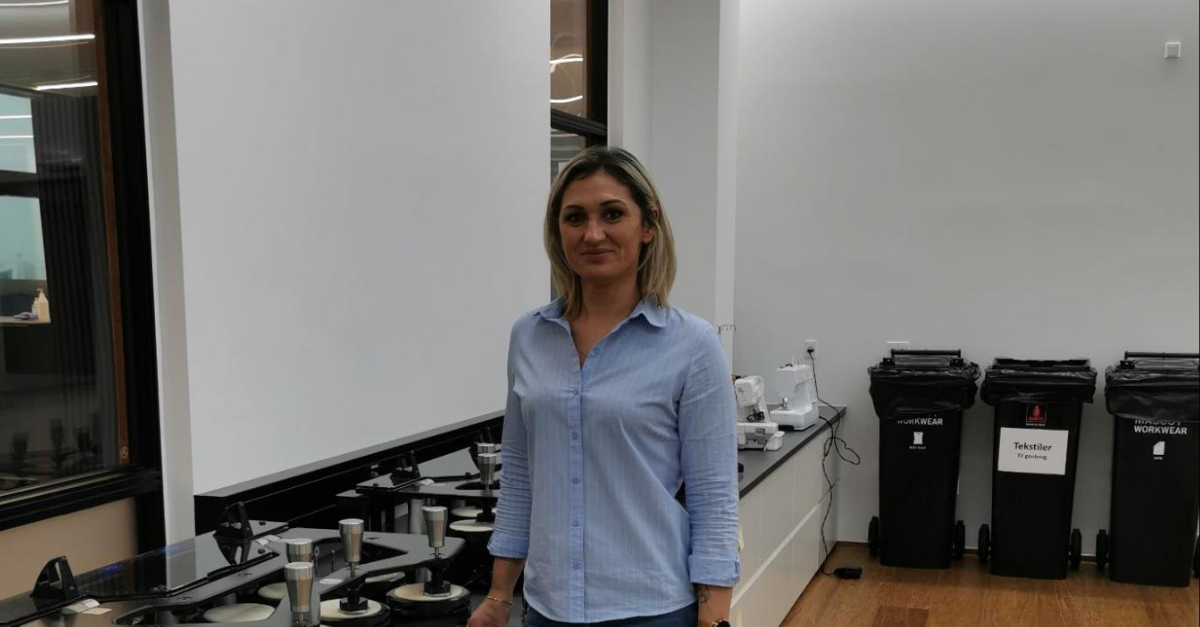
The test types vary, but most of the tests performed at the brand’s Denmark laboratory, are traditional testing such as abrasion, pilling, colour fastness, and strength testing. “Colour fastness is key, as we want to understand whether our products will wash the right way and continue to perform for their intended purpose.”
More recently, added Henrik, the brand has conducted more frequent testing for stretch and recovery, elongation, tear testing, and hydrostatic head testing, which is an important assessment for the efficacy and performance of protective clothing.
Crossing the line: Where functionality meets fashion
The “workwear” style - influenced by jobs involving manual labour - has influenced the fashion industry for decades, particularly the streetwear trends of wearing heavy leather boots, ripped jeans, cargo trousers, lumber jackets, dungarees and corduroy [Source].
Yet the recent move for Mascot to conduct more performance-based testing has been driven by market trends, where fashion and style is influencing the design and specification of performance wear such as workwear and PPE.
“The influence of fashion and design has penetrated the sportswear and activewear market, and we’re seeing it in our sector, too,” explains Henrik. “Consumers who work in a wide spectrum of industries are demanding their workwear be not only stylish and fashionable, yet comfortable and safe.”
With wearer comfort being key, the use of high performance fabrics with moisture management and thermal regulation properties has become widespread, and are strong selling points for brands making such claims on their garments. Tests like 4-way stretch have become an important part of day to day R&D and QA testing on Mascot’s products, to ensure their garments follow the movement of the body in real-life scenarios, to provide comfort as well as functionality.
Why Mascot chose James Heal
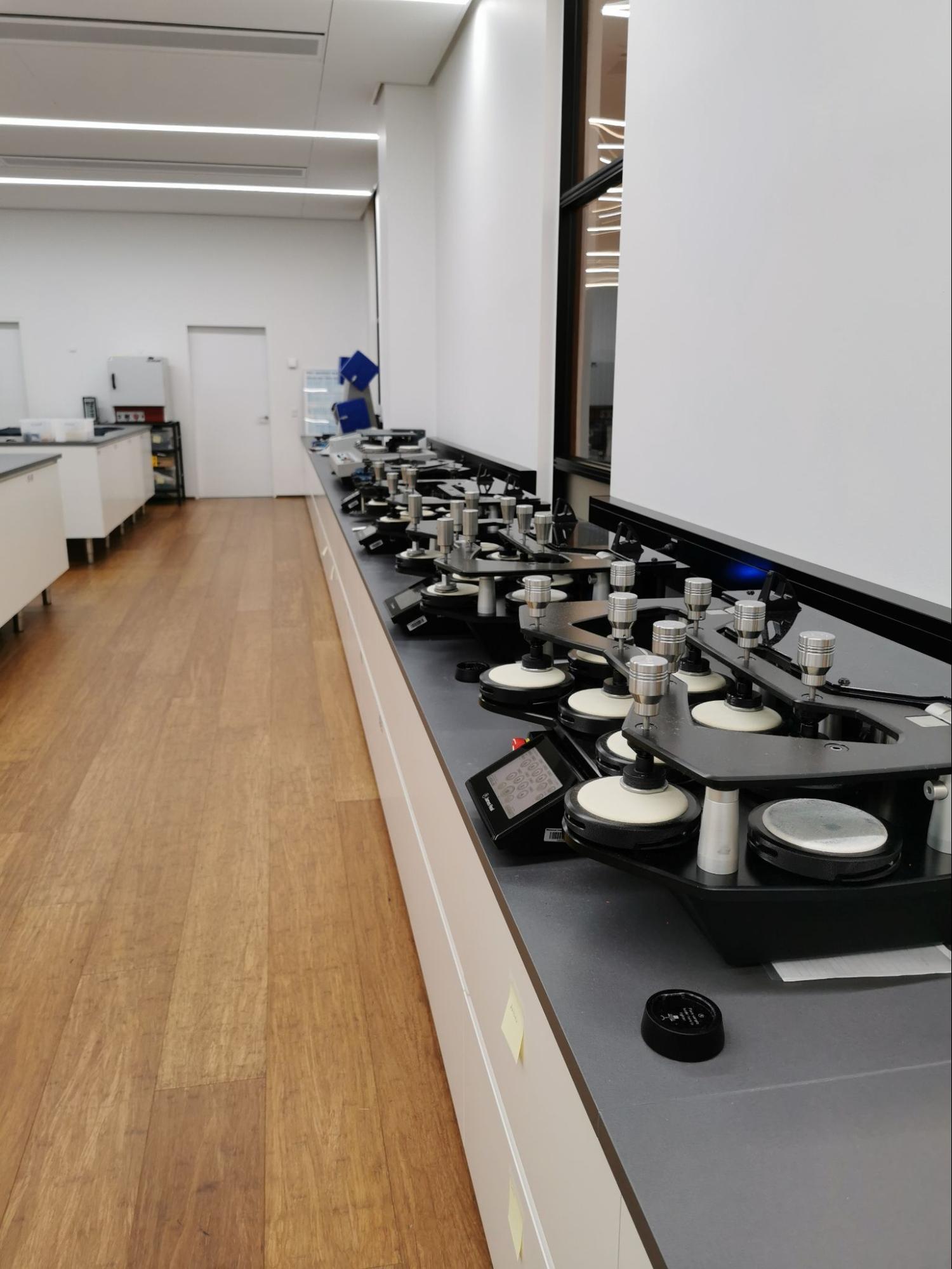
Henrik, Lab Coordinator at Mascot“The Martindales are sublime! We have five in our lab at the moment"
With a 20 year long relationship, Mascot has chosen James Heal time and again as their brand of choice for textile testing, says Henrik. “James Heal has always been our first choice, and will continue to be. The pricing has always been reasonable, and the customer service and technical support has been vital to us.”
When asked about his favourite James Heal instrument, Henrik explained that “the Martindales are sublime! We have five in our lab at the moment. We’ve never had an issue, they help to maximise our lab operators’ efficiency when using the 9 station Martindale - we can increase throughput by running the machine overnight, saving time without needing to change samples as the instrument has 9 stations to work with.”
Henrik explains that Mascot is always happy to recommend James Heal to their suppliers “this is what we do when our fabric suppliers visit us - we show them the lab, we tell them to use James Heal. Our lab is like a showroom for them to see the machines running and what ‘best practice’ looks like for training and development.”
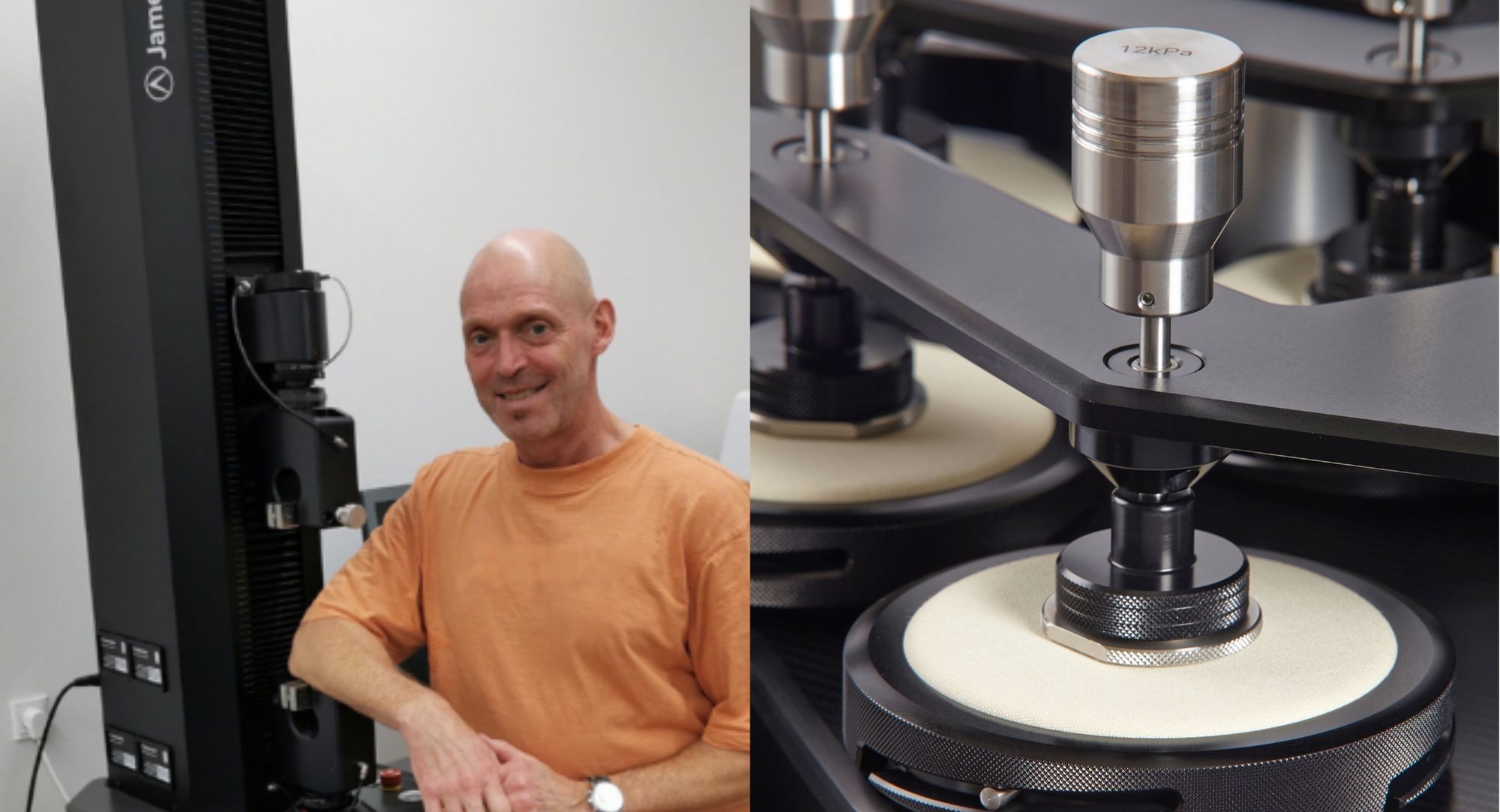
Impact of sustainability
Consumer perception on comfort and style is one of the key trends having a major impact on the personal protective clothing industry. However, there is also a strengthening commitment throughout the supply chain to sustainability. Henrik understands how crucial sustainability is in the industry, and to Mascot as a brand. Being a more sustainable company and industry is a positive step forward; yet also presents a challenge, emphasises Henrik.
“Switching to more environmentally sustainable materials, such as recycled, may be less effective in terms of fabric/garment performance. This is something that we are investing time in, conducting tests to better understand the efficacy of these fabrics, to ensure our garments continue to meet the wearer’s needs and expectations on comfort, safety and performance.”
Future outlook
When asked ‘what does the future hold?’ for the industry, Henrik says he expects to see an increased demand for PPE which performs a plethora of functions and offers durability “without sacrificing style or comfort.”
As a result, he says, “innovation in the industry will continue by focusing on enhancing the comfort properties of PPE clothing, creating more fashionable styles, and producing materials using sustainable raw materials and processes.”
As a longstanding supplier to Mascot, we are always delighted to support Mascot with their textile testing needs, and play a crucial role in their R&D activity testing new materials and trends.
Enjoyed this article?
We’ll be sharing more customer stories and insights on our blog - keep checking for updates, or subscribe to our email newsletter here.