In this customer case study, we spoke to Sabrina Mimoune, Quality Manager and Alan Badrov, Lab Manager at French company Balas Textile, to discuss the importance of testing technical textiles and their experiences using James Heal’s instruments.
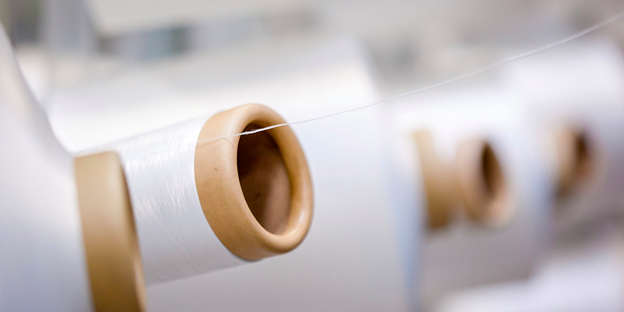
A leader in technical fabric production
Balas Textile is a manufacturer of technical textiles, specialising in the production of water repellent and technical fabrics, primarily serving the military, PPE, luxury goods and sports apparel sectors. Balas Textile is vertically integrated with its own in-house testing laboratory, along with weaving and knitting. However, Balas Textile does not manufacture clothing, it provides fabrics that will be used in the manufacture of the final garment.
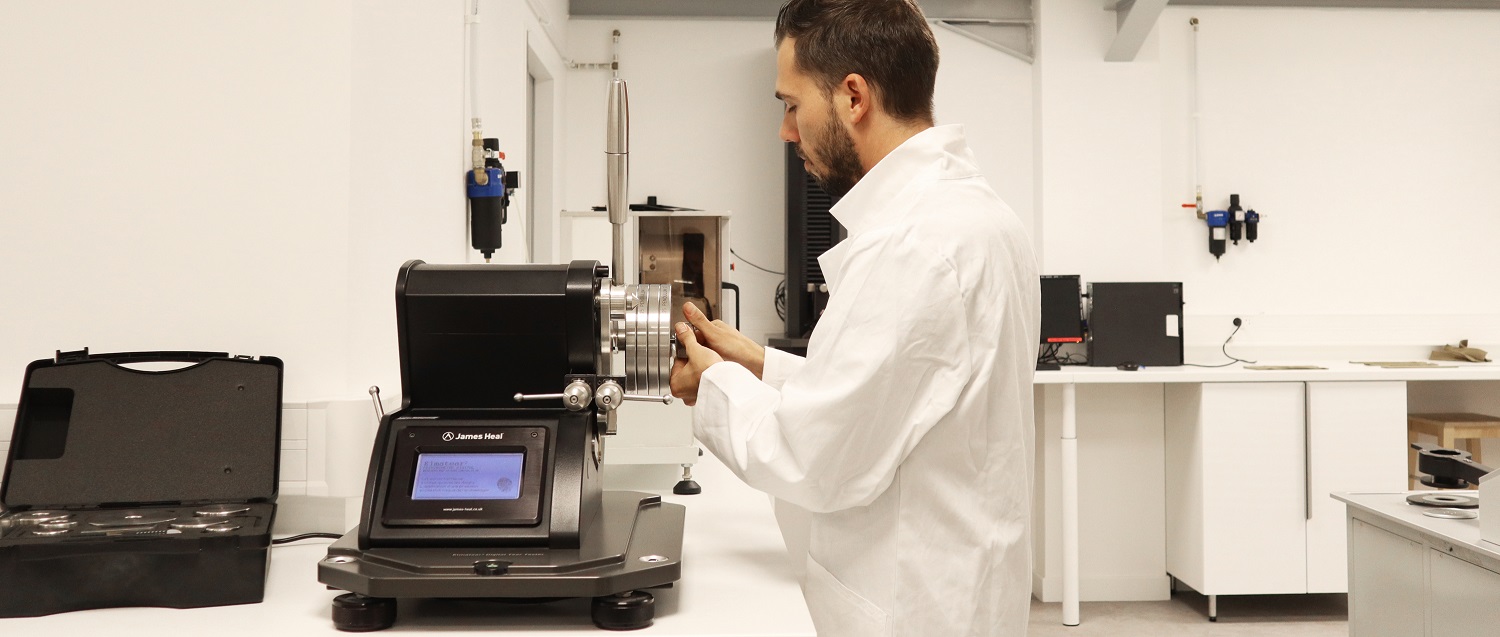
Sabrina Mimoune, Quality Manager“We undertake a number of different test types. From physical properties, to laundering, comfort testing to torque testing.”
In-house laboratory for reactive and proactive testing
Sabrina has worked in the Balas Quality Department for the last three years, and Alan has held the role of lab manager for four years. During this time, the company has re-developed its in-house textile testing capability and invested in an internal laboratory for R&D as well as quality and production testing. Working closely with James Heal’s channel partner in France, Balas Textile chose to equip the lab with James Heal instruments, due to their trust in the brand and the quality of the instruments.
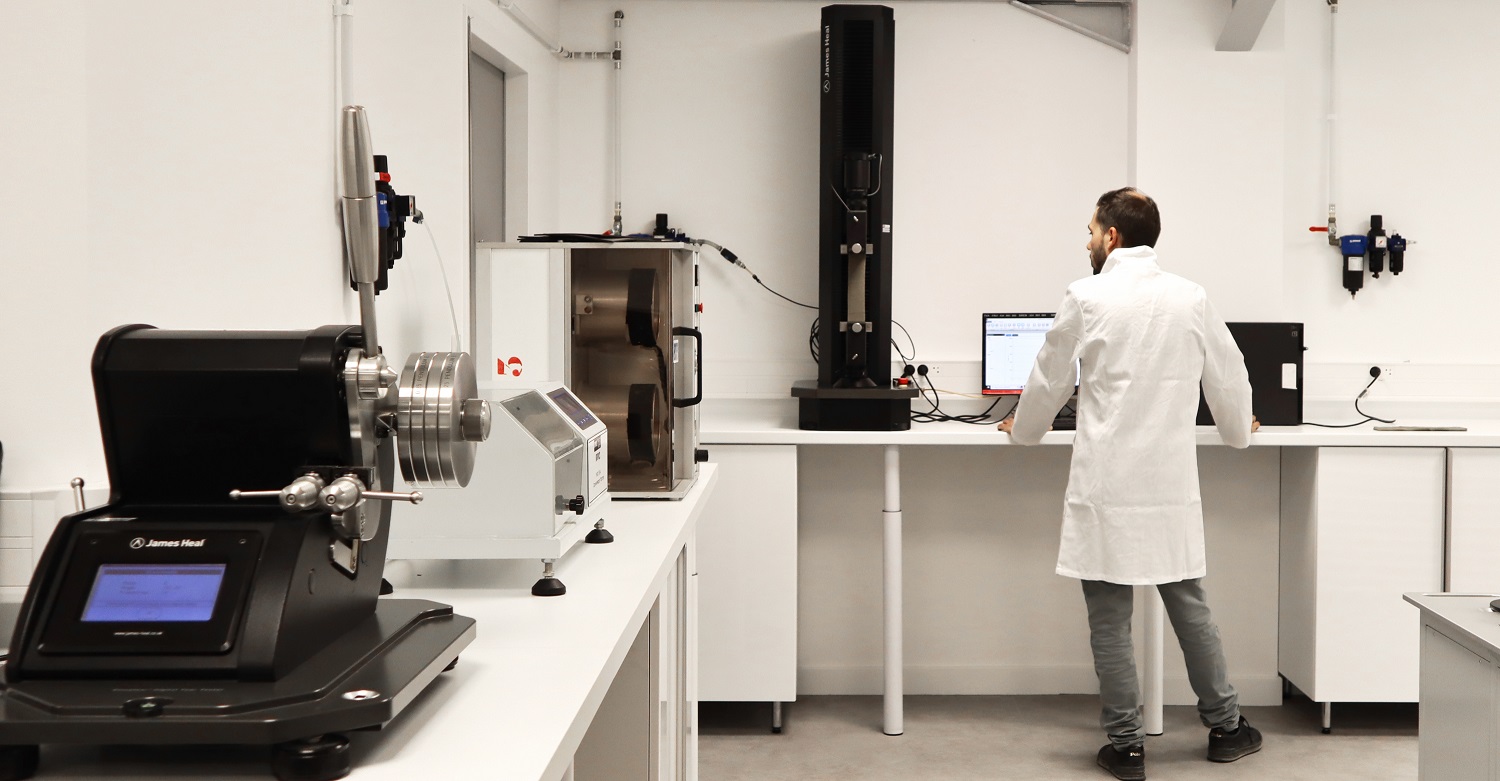
Instruments used in the Balas Textile Lab
Balas Textile use a number of James Heal textile testing instruments in their laboratory including:
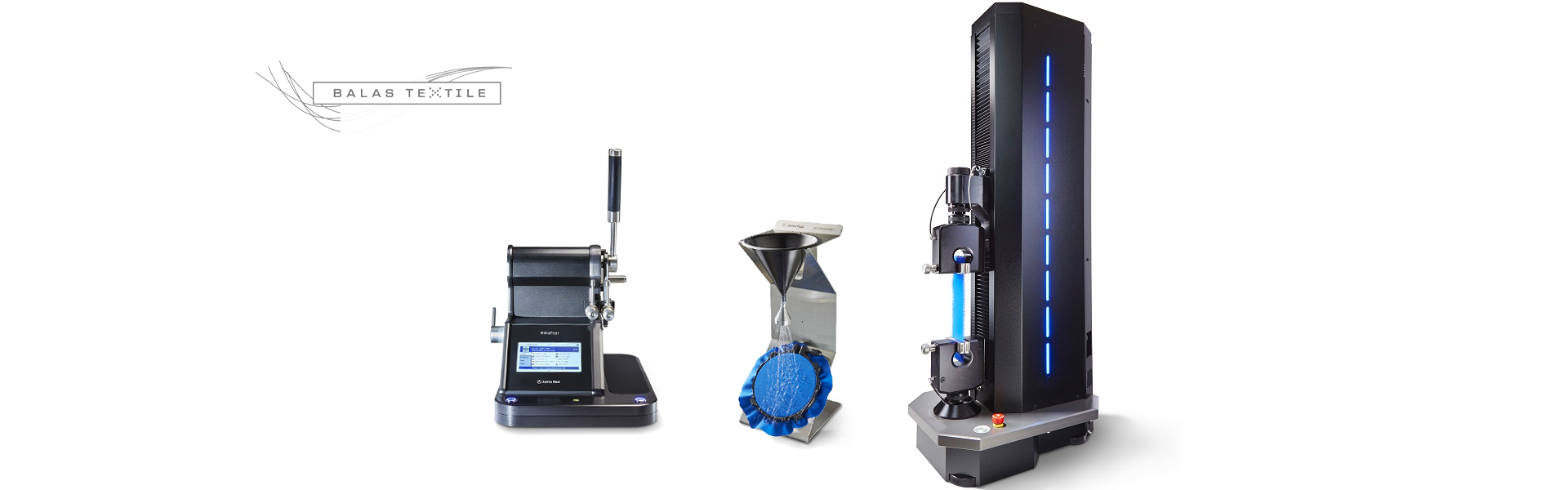
“We are very happy with the knowledge and support provided by James Heal and VVC,” says Alan. “We consider VVC a very important partner, as we trust that they will follow our journey to continuously improve the laboratory. We can rely on the support from both VVC and James Heal for technical requirements. We always get quick responses and strong support.”
With a vision to continually evolve and improve the lab, says Alan, Balas Textile plans to triple the size of the lab in the coming year and need more testing equipment. “It is of no question that we will continue to work with VVC and we will specify James Heal instruments for their exceptional quality and precision”, added Alan.
An evolution in demand
Sabrina says that Balas Textile has seen a surge in demand from the international military sector, who are exploring ways to make military textiles more durable whilst prioritising safety and comfort. The latter focusing on making the materials more lightweight yet robust, and more breathable with good moisture management and wicking properties. Furthermore, personal protective fabrics have been a growing category for the manufacturer, says Sabrina, with a rise in fashion influence in the design and fit of PPE, and more awareness of ‘feeling good’ and prioritising wearer comfort.
Alan Badrov, Lab Manager“Having an in-house laboratory has been fundamental to Balas Textile being able to respond rapidly to market demand, allowing us to quickly focus our R&D testing on new fabrics such as anti-stain technology or odour-resistant fabric, using the lab for exploring new and novel materials.”
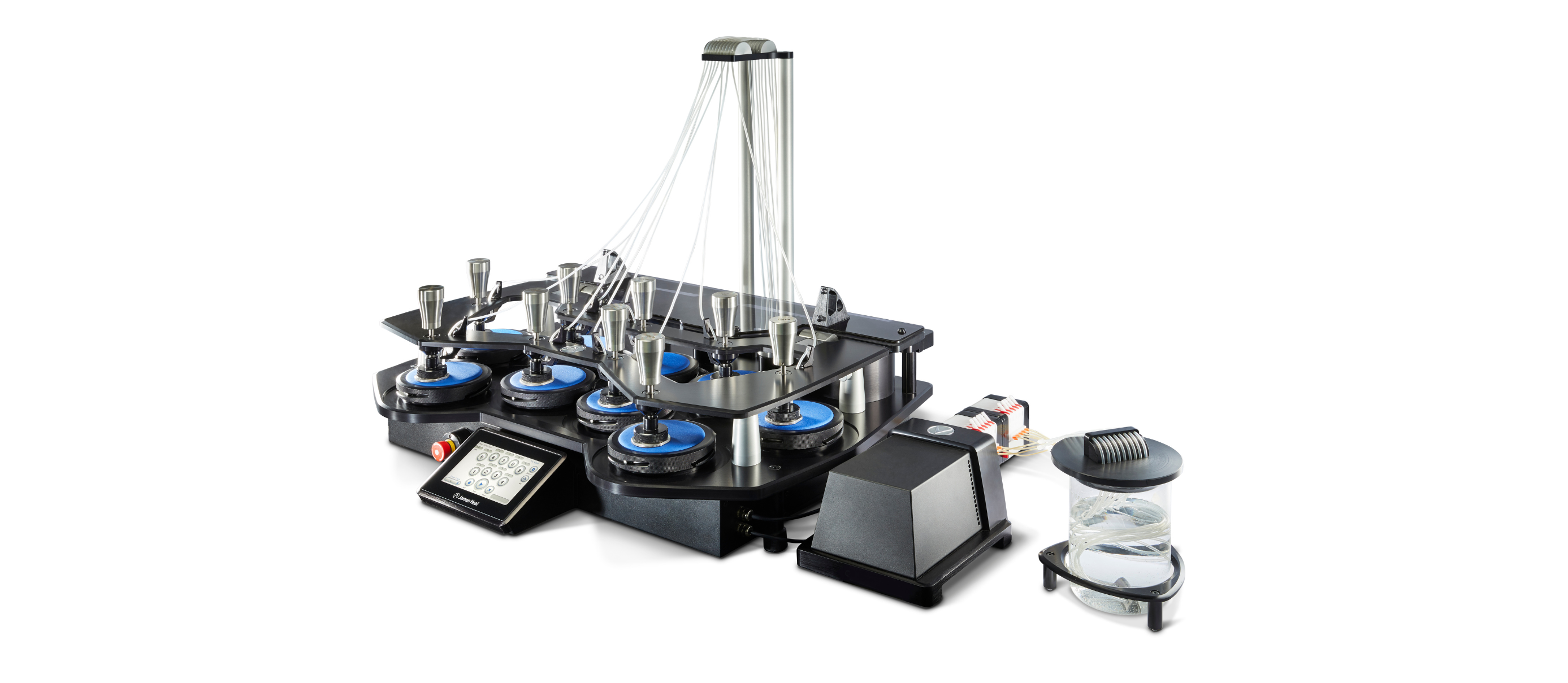
Early adopters of new technology
A good example of the Balas Textile approach to R&D was being one of the first textile manufacturers to purchase a James Heal Aquabrasion testing instrument in 2019. The Aquabrasion is a wet abrasion tester based on the traditional Martindale instrument. It uses a controlled pump system to dose fabric specimens with liquid which keeps the specimen wet for the duration of the test. De-ionised water can be used to replicate rain, or a perspiration solution can be used to replicate sweat.
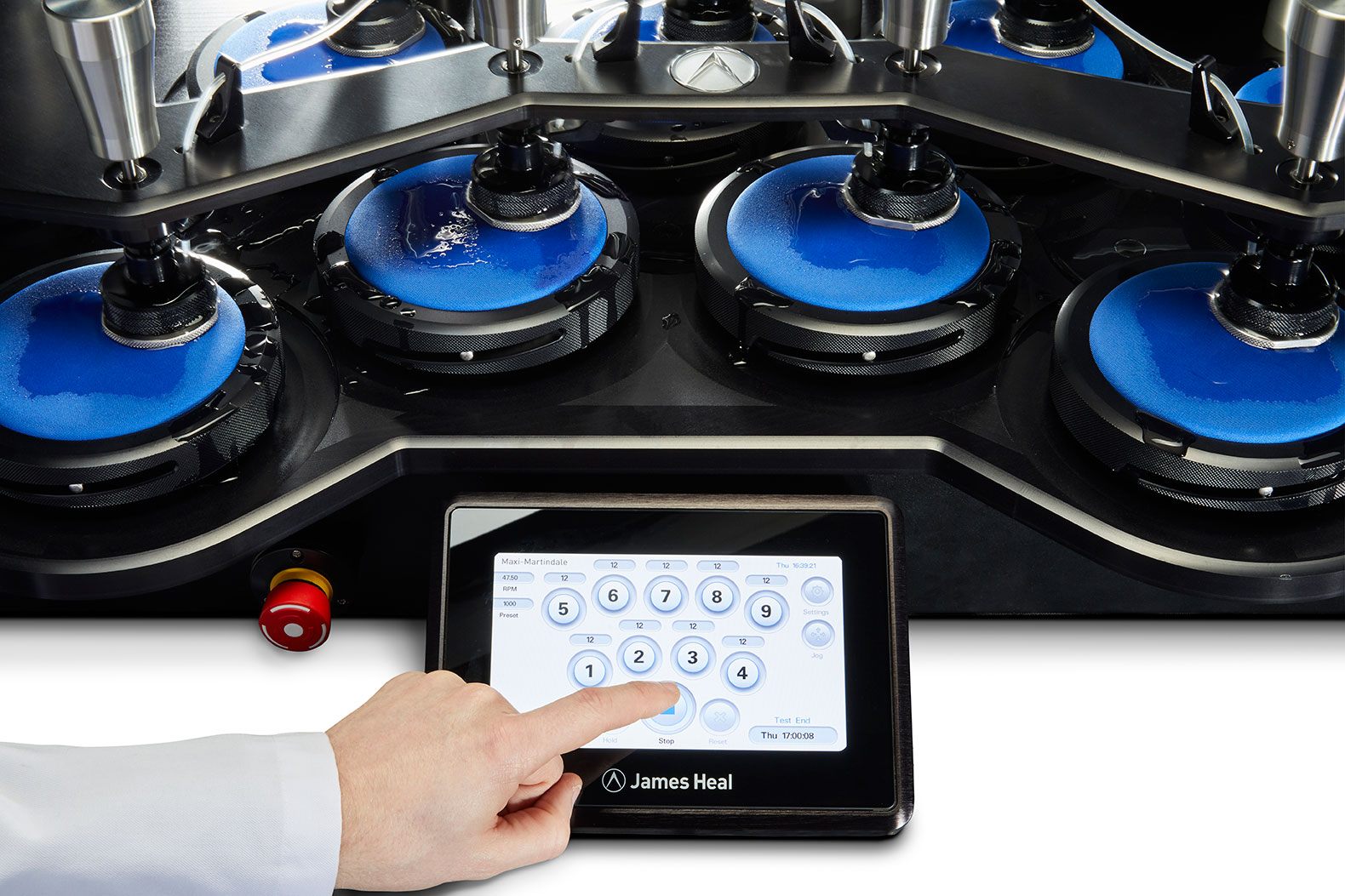
“Testing for abrasion under wet conditions is a very interesting concept,” comments Alan. “We were intrigued to try this out and test our swimwear materials using the Aquabrasion, rather than a tensile tester, using the standard abrasion test (ISO 19247-2).”
So far tests have been conducted continuously using only tap water. The next step with Aquabrasion, adds Alan, is to test using chlorinated water as well as perspiration, to explore the impact these have on the material’s performance in true ‘user’ conditions.
According to Sabrina, the Aquabrasion has attracted a lot of interest from visitors to the internal laboratory, with many questions about the machine’s purpose and applications.
“We have found that the Aquabrasion is versatile as it can be adapted to specific use cases. It is an accurate and precise alternative to how we’ve tested materials before, such as swimwear. We’ve gained much more insight into real-life conditions than with other instruments we have used to conduct this test method before.”

And finally
In conclusion, Balas Textile has made significant investment in expansion of the lab and testing facilities, making improvements in energy consumption and purchase of new equipment amounting to almost €400,000 in 2022, further strengthening their partnership with VVC.
VVC Sales Manager Grégoire Ghilbert added, “Balas Textile is a long-standing partner of VVC. Our collaboration around the development of their laboratory and the calibration of their equipment are always extremely constructive and allow our mutual teams to develop their skills.
It is with pleasure that VVC continues to accompany Balas Textile in the implementation of new performance wear tests such as Aquabrasion.”